Not at your computer? It’s easy to manage your forum on your phone. Create, delete and rearrange posts, or share them on social media. Enable/disable your comments and more.
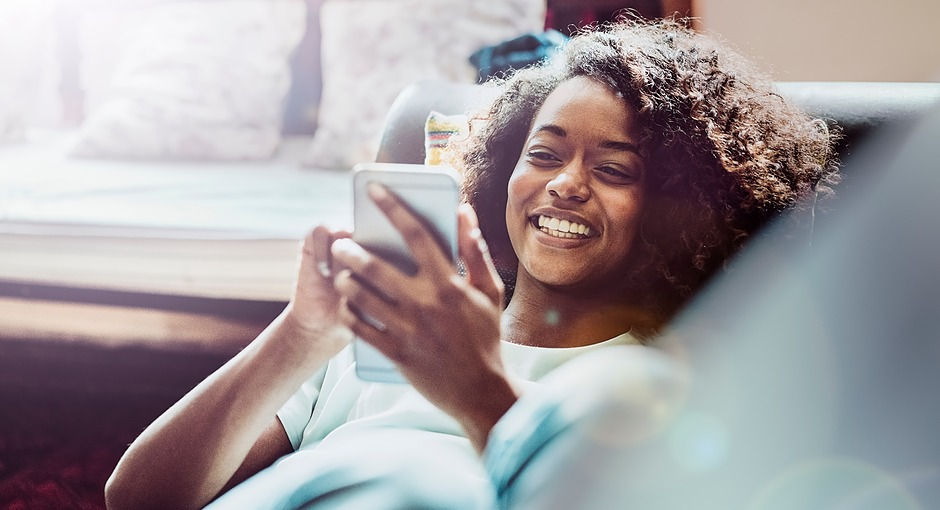
You can also pin your favorite posts so more people will see them and they get more engagement within your forum’s community.
Because Wix Forum is so mobile friendly, once your forum is set up, all you need is your phone.
Regenerative combustion technology has been used in large-scale and high-temperature furnaces such as blast furnace hot blast stoves, open hearth furnaces, coke ovens, and glass melting furnaces since the mid-19th century. Optimal Vacuum Heat Treatment For Bevel Gears The principle is to use the waste heat recovery device in the regenerator to alternately switch the flue gas and air to make it flow through the regenerator, so as to recover the sensible heat of the high-temperature flue gas to the greatest extent and increase the temperature of the combustion-supporting air. However, the traditional regenerator uses checker bricks as the regenerator, which has low heat transfer efficiency, large regenerator volume, and long reversing cycle, which limits its application in other industrial furnaces.Vacuum Hardening Stainless Steel The new type of regenerator adopts ceramic balls or honeycomb as the regenerator, and its specific surface area is as high as 200-1000m2/m3, which is dozens to hundreds of times larger than the old checker bricks, thus greatly improving the heat transfer coefficient. The volume of the regenerator can be greatly reduced. In addition, due to the improvement of the reversing device and control technology, the reversing time is greatly shortened. The reversing time of the traditional regenerator is generally 20-30 minutes, while the reversing time of the new regenerator is only 0.5-3 minutes.Sintering of B4C by Pressureless Liquid Phase Sintering The new regenerator has high heat transfer efficiency and short reversing time, resulting in low exhaust gas temperature (below 200°C), and high preheating temperature of the preheated medium (only 100-150°C lower than the furnace temperature). Therefore, the waste heat of the exhaust gas is recovered close to the limit, the temperature efficiency of the regenerator can reach more than 85%, and the heat recovery rate can reach more than 80%.Vacuum Heat Treatment of Fasteners